Powder Metallurgy: Revolutionizing Knife Blade Manufacturing
Powder metallurgy, a cutting-edge manufacturing process, revolutionizes knife blade production by tr…….
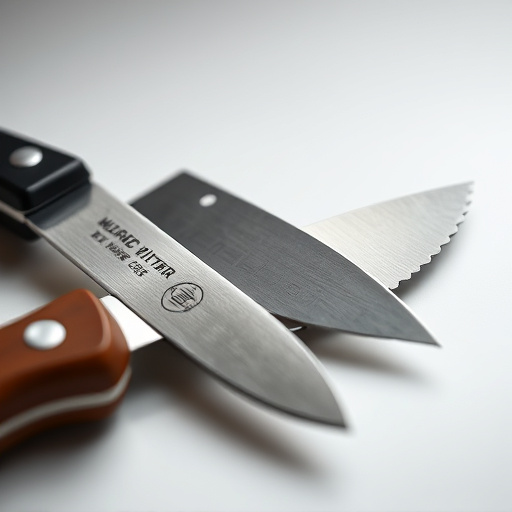
Powder metallurgy, a cutting-edge manufacturing process, revolutionizes knife blade production by transforming metal powders into complex shapes with superior mechanical properties. Through pressing and sintering, this technique creates high-performance blades with enhanced strength, fine microstructures, and precise geometries, surpassing traditional casting or forging methods. Powder metallurgy offers unparalleled precision and customization, enabling the production of complex designs and high-alloy blades tailored for hunting, slicing, tactical use, healthcare, food processing, and defense applications. While challenges exist in achieving optimal microstructure and addressing finishing issues, continuous research aims to unlock the full potential of this game-changing technology in knife blade manufacturing.
Powder metallurgy is a revolutionary process transforming the way knife blades are crafted. This advanced technique fuses fine metal powders under high pressure or heat, creating intricate structures with superior strength and precision. In this article, we explore the intricacies of powder metallurgy in knife blade manufacturing, delving into its process, benefits, material types, applications, and the challenges it faces. Discover how this technology is shaping the future of sharp tools.
- What is Powder Metallurgy?
- The Process of Creating Knife Blades Using Powder Metallurgy
- Advantages of Powder Metallurgy for Knife Blade Manufacturing
- Types of Materials Used in Powder Metallurgy Knife Blades
- Applications and Uses of Powder Metallurgy Knife Blades
- Challenges and Limitations of Powder Metallurgy in Knife Blade Production
What is Powder Metallurgy?
Powder metallurgy is a manufacturing process that shapes metal powders into complex shapes and structures through compression and sintering. This advanced technique allows for the creation of intricate parts, including knife blades, with superior mechanical properties. By starting with fine metal powders, this method enables the production of items with precise geometries and enhanced performance compared to traditional casting or forging methods.
The process involves mixing the desired metal powders, often in combination with binders, to create a compactsible material. This mixture is then compressed under high pressure into the desired shape. Subsequent sintering, usually involving heat treatment, fuses the particles together, forming a solid structure. Powder metallurgy is particularly advantageous for knife blades, offering benefits such as improved strength-to-weight ratio, fine microstructures, and freedom in designing complex geometries to enhance performance and durability.
The Process of Creating Knife Blades Using Powder Metallurgy
Powder metallurgy offers a unique and innovative approach to crafting knife blades, revolutionizing the traditional manufacturing methods. The process begins with carefully selected metal powders, which are mixed and pressed together under high pressure to form a compact shape known as a green body. This step is crucial in creating the intricate geometry of knife blades, allowing for complex designs that would be challenging or impossible to achieve with solid-state processing.
Once the green body is formed, it undergoes sintering, a heat treatment process where the powder particles fuse and bind together to create a solid blade structure. The precise control over temperature and time during sintering ensures the desired mechanical properties of the knife blade, such as hardness, toughness, and strength. This method enables the production of high-performance knives with exceptional edge retention, durability, and precision, catering to both industrial applications and everyday carrying needs.
Advantages of Powder Metallurgy for Knife Blade Manufacturing
Powder metallurgy offers several significant advantages for knife blade manufacturing, making it a preferred process in this industry. One of its key benefits is the ability to create complex and intricate designs with high precision. By pressing and sintering powdered metals, manufacturers can produce blades with unique shapes, edge configurations, and internal structures that are difficult or impossible to achieve using traditional casting or forging methods. This level of customization allows for the design of highly efficient and performance-oriented knife blades tailored to specific applications, such as hunting, slicing, or tactical use.
Additionally, powder metallurgy enables the production of high-performance alloys with excellent hardness, wear resistance, and edge stability. The process facilitates the incorporation of various elements and their precise control at the microlevel, resulting in blades that exhibit superior cutting ability and longevity. Moreover, this manufacturing technique can create uniform density and eliminate internal stresses commonly found in cast or forged blades, ensuring consistent quality and reducing the risk of cracking or bending under stress.
Types of Materials Used in Powder Metallurgy Knife Blades
In powder metallurgy, the production of knife blades involves unique considerations due to the specific properties required for cutting edges. The process leverages advanced manufacturing techniques to create complex shapes and precise geometries from fine metal powders. Common materials used in this application include high-carbon steels, tool steels, and even ceramic composites. High-carbon steels, known for their exceptional hardness and edge retention, are often chosen for knife blades, offering the necessary sharpness and durability.
Tool steels, such as A2 or D2 steel, are also favored due to their ability to maintain an edge while withstanding impact and pressure. Ceramic composites, though less conventional, are gaining traction for their lightweight nature and extreme hardness, making them suitable for specialized knife applications requiring corrosion resistance and low maintenance. These materials’ unique properties are optimized through sintering, pressing, and other powder metallurgy techniques to produce knife blades that combine strength, sharpness, and longevity.
Applications and Uses of Powder Metallurgy Knife Blades
Powder metallurgy has found its way into various industries, and one notable application is in the production of knife blades. The process involves compacting a fine powder of metal or alloy under high pressure to create solid, dense parts, including knife blades. This method offers numerous advantages for blade manufacturing; it allows for complex geometries and precise control over material properties, enabling the creation of blades with enhanced durability and edge retention.
Powder metallurgy knife blades are sought after in sectors like healthcare, food processing, and defense due to their superior strength-to-weight ratio and resistance to corrosion. The technique can also incorporate hard metals and alloys, resulting in blades with exceptional hardness and wear resistance. This technology has revolutionized the design and performance of knives, catering to specific applications where traditional casting or forging methods may fall short.
Challenges and Limitations of Powder Metallurgy in Knife Blade Production
Powder metallurgy, while offering innovative possibilities in manufacturing, faces challenges and limitations when applied to knife blade production. One significant hurdle is achieving the required microstructure and mechanical properties. Knife blades demand a fine balance of hardness, toughness, and edge stability, which can be difficult to reproduce consistently through powder metal processes. The sintering conditions, particle size distribution, and composition all play crucial roles in determining the final properties, making precise control and optimization essential but complex.
Additionally, the porosity and surface quality of blades produced by powder metallurgy can be issues. High porosity can weaken the structure, while rough surfaces may require extensive finishing to meet the desired aesthetics and functional standards. These limitations necessitate continuous research into advanced sintering techniques, material compositions, and process controls to overcome the challenges and fully harness the potential of powder metallurgy in crafting high-performance knife blades.
Powder metallurgy has emerged as a revolutionary process for manufacturing high-performance knife blades, offering numerous advantages over traditional methods. By leveraging fine metal powders, this advanced technique allows for precise control over blade composition and microstructure, resulting in exceptional edge hardness, durability, and corrosion resistance. The versatility of powder metallurgy enables the production of knives with unique designs and specialized materials, catering to diverse applications from culinary arts to industrial cutting. While challenges remain, such as porosity issues and material homogeneity, ongoing research and advancements promise to further refine this technology, ensuring its place as a game-changer in knife blade manufacturing.